I have an old Honeywell 4-way China hat from an old Huey Debolestis gave me that feels the way you d
I have an old Honeywell 4-way China hat from an old Huey Debolestis gave me that feels the way you describe. I think it's a period specific thing? ..same era as Phantom but modern ones have shorter throws.
All the 4.3mm tacts have pretty short throws by themselves but where they're located on the lever makes the hat throw much longer but reduces force considerably, which is why the common 260gf ones feel so soft. 500gf is still a bit light but much better feeling.
17 Replies
Ah. That makes sense. I wonder if it would be possible to create a design that gangs up the switches in parallel so that you get 500+gf actuation at the grip?
The Alps feel softer to me than the 260gf ones but also have super short shafts and throws on par with minsticks so kinda the worst of both worlds imo. Great for confined installations I suppose since they're compact
An interesting idea. Another would be to use some kind of elastomer to work against so your squeezing a rubber spring at the same time as the plunger to get more force. hmmm
If anyone is trying to do a direct drive setup I have tested the Planetary Gearbox below and it works. I went with the 10:1 version and @walmis standard motors. 10:1 is too much reduction. I would recommend the 5:1. I didn't notice much backlash, but they make a more expensive version that has less backlash. One note the shaft on VPforce motors is longer than the gear reduction input will accept. Just keep that in mind you will need a spacer or you can sandwich the motor and gearbox around a mounting plate like I did.
https://www.omc-stepperonline.com/plm-series-planetary-gearbox-gear-ratio-10-1-backlash-30-arc-min-for-8mm-shaft-nema-23-stepper-motor-plm23-g10-d8
PLM Series Planetary Gearbox Gear Ratio 10:1 Backlash 30 arc-min fo...
This high-precision planetary gearbox is belong to PLM series gearbox, it with gear ratio 10:1 and a maximum 30arc-min backlash. Diffent with the PLE series' steel gears, PLM series' gears are made of powder metallurgy. It's an excellent choice for applications that require good accuracy but low cos
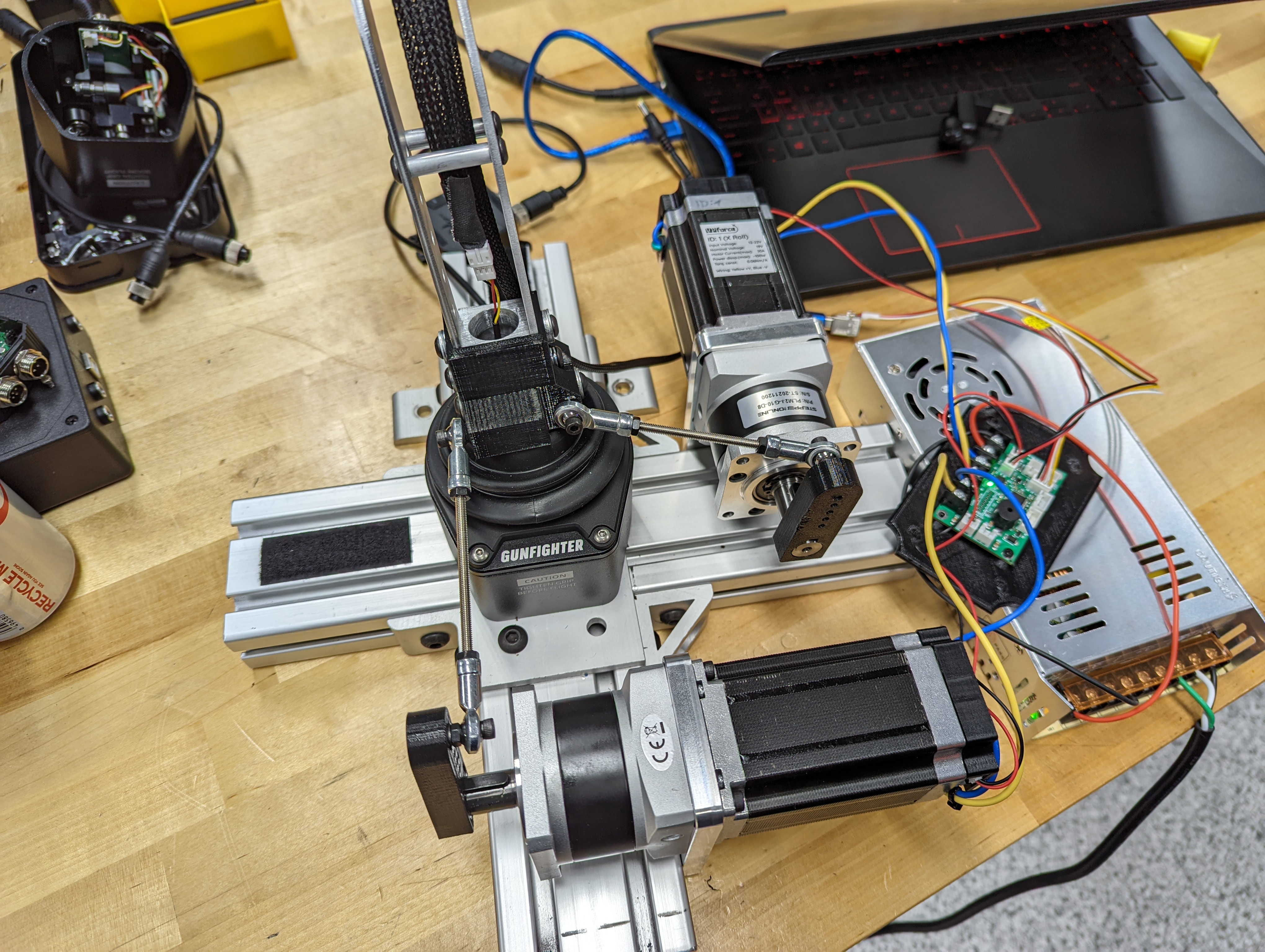
neat! that looks great.
Interesting. .5deg still sounds like too much backlash, at least for a full length stick though it's worth noting most light aircraft have a little to a lot of backlash in the controls irl. What's the arc-min rating of the higher end one?
<= 15 arcmin is the lowest spec i can find on their site.
15 arcmin ~= 1mm backlash w/ 250mm extension.
Heh was just calculating it for 300mm. Even at 30arcmin that's only 3mm which is still within the allowed slop spec'd in the maintenance manual of the glider I fly
I'm lazy so i just drew two lines in cad and put an angle constraint ;)
I'm lazier :p https://www.blocklayer.com/riserun.aspx
I'll put an indicator on the version I have when I get home and get an accurate measurement. I'm just using 3d printed arms on it right now (waiting for a broach to show up) and have a 24" cyclic extension. During use there is enough flex in the whole setup that the backlash was undetectable at the grip. Once the aluminum arms are done I will report back. The version below is rated at 3 or 5 Arcmin depending on ratio. I didn't want to wait for them to arrive from China.
https://www.aliexpress.com/item/1005001310958833.html?spm=a2g0o.detail.1000023.16.4efe4548zaGKXd
aliexpress.com
82.57US $ 32% OFF|Helical Gear Nema23 Planetary Gearbox High Precis...
Smarter Shopping, Better Living! Aliexpress.com
Not cheap but damn that's precise and I'm sure quite economical vs an American of German version of the same thing lol. For people with more money than space it seems like a great option vs belts. 10:1 doesn't seem unreasonable either, you lose 10% of the input torque for one but Walmis tested the system at 24:1 already with no adverse affects. Might make 'backdriving' the system misbehave though?
Another alternative for belt drive is 'shaft winding' where you drill a cross-hole in the drive shaft or hub and run a steel cable through it with 4-5 wraps either side of the hole before connecting to the final pulley. It's how Roland van Roy did his yoke as seen below. it's used irl too though, my boss at the motion platform place I used to work (E2M Technologies) worked on the Air Force 1 Blackhawk simulator and it was used on some of the axes there.

Advantage of shaft winding vs belts is compactness and cost. You can use very small drive side which really reduces the overall size considerably by the time you get to the final
I hadn't really been aware of shaft winding. does it also potentially counter the elasticity of belts? I assume you'd still need a tension system so some flex would be added.
Sort of? Steel cable also has its own elasticity. You need *some kind of tensioning system though it doesn't need to be complicated, just something to get it close enough to final the tension by moving the motor like you would a belt system. Alternative to steel cable is Dyneema/Spectra etc which has much higher load caps per thickness than steel but only like 1% stretch (vs steel cable's 20%) @50% break strength
The shaft winding looks like a good idea to explore. 10:1 with my setup and power supply was more than enough for a cyclic setup. Once I have the aluminum arms done I will test the spring effects. I'm running ~5% on damper and 10% on friction at 50% total output. Holds perfectly in place and feels really good.
The runs of these are very short though so even steel cable feels solid
I guess it would depend on the size of the steel cable vs the size of the belt.