45 degree or 90 degree trace which is preferable when routing a pcb trace
I am designing a PCB board, which angle is generally preferable 45 or 90 degrees and why. And how does it affect the overall PCB performance? Are there any scenarios where one angle maybe more advantages than the other? Which one is more prone to signal integrity issues? Need your help on this?
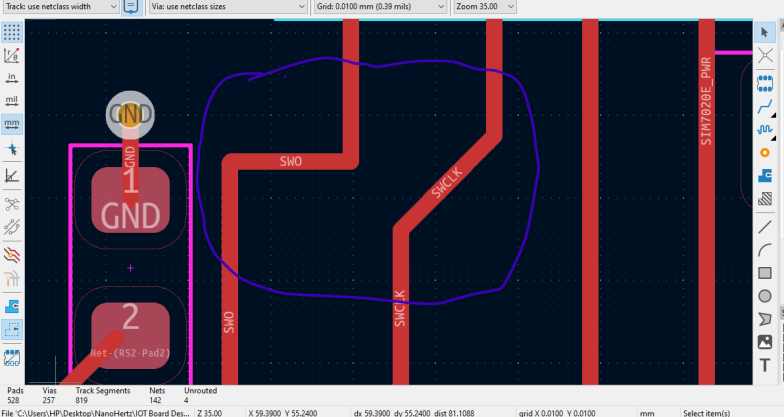
6 Replies
45 degree is generally preferable, is has lesser chances of causing signal integrity issues in High Speed PCB design
In Low speed designs 90 degree trace might not be necessary an issue, but it is essential to follow good pcb design practices when doing your pcb layout. So it is necessary to use 45 degrees in your designs.
Consider the specific requirements of your design, especially if it involves high-speed signals. In such cases, using 45-degree angles can contribute to better signal integrity. However, in low-speed or less critical designs, 90-degree angles may offer simplicity and cost advantages without significant drawbacks.
How can 90 degree trace bring about cost advantage in the design
Using 90-degree traces in PCB design can bring about cost advantages due to several reasons:
Manufacturing Efficiency: Right-angle corners can be challenging for the etching process in PCB manufacturing, potentially requiring additional steps and precision. 90-degree angles are more easily accommodated in the manufacturing process, reducing the likelihood of errors and improving overall efficiency.
Reduced Production Time: The manufacturing equipment and processes are often optimized for simpler geometries, which include 90-degree angles. Using 90-degree traces can lead to quicker production times, contributing to cost savings.
Lower Fabrication Costs: Some PCB manufacturers might charge more for designs with tighter tolerances, including sharp angles. Using 90-degree traces can fall within standard manufacturing tolerances, helping to keep fabrication costs lower.
Minimized Signal Integrity Issues: Sharp corners in high-speed digital signals can lead to signal integrity challenges, such as reflections and impedance mismatches. Using 90-degree traces can help mitigate these issues, reducing the need for additional signal conditioning components or design iterations.
Ease of Design: Designing with 90-degree traces is often simpler and more straightforward. It can reduce the complexity of the layout process, making it easier for designers to achieve their goals without sacrificing performance.
It's essential to consider the specific requirements of your design and manufacturing processes to determine the most cost-effective approach. While 90-degree traces can offer advantages, the overall impact on cost may vary based on the complexity of the PCB and the capabilities of the manufacturer.
Cost isn't really much of a factor in designing trace angles, one thing we can say that affect the cost in routing pcb traces are the trace spacing or width. When you go beyond the manufacturers capability then, you will be charged higher for your design. Some manufacture do design a rounded corner trace mostly use in RF and Highspeed Designs, and designing the trace angle do not add much in the cost.
Anyone has any viewpoint on this ?
You're absolutely correct. While trace angles, particularly 90-degree angles, can impact the manufacturing process, the primary factors influencing cost often revolve around trace spacing, width, and adherence to the manufacturer's capabilities. Manufacturers typically have specific guidelines and capabilities for trace dimensions, and exceeding these can result in higher costs.
Trace width and spacing directly affect the precision and complexity of the manufacturing process. Narrow traces and tight spacings may require more advanced manufacturing techniques, adding to the cost. On the other hand, adhering to standard design rules and manufacturing capabilities can help keep costs within reasonable limits.
It's essential for designers to be mindful of the manufacturer's specifications and guidelines, optimizing the design for manufacturability while balancing other considerations like signal integrity and performance. Making design choices within the manufacturing capabilities not only helps control costs but also contributes to a more efficient and reliable production process.